Research & development, innovative thinking, and optimization are all hallmarks of the organizational culture in manufacturing industries. To develop products at a rapid pace, it is heavily reliant on employees’ skill set with heavy machinery.
Even so, there is a significant gap when it comes to soft skills such as good communication, employee satisfaction and trust, and leadership. Manufacturing employees are traditionally the least engaged at work, according to a Gallup report, with three-quarters of workers disengaged.
Organizational Culture In Manufacturing Industries
Employee engagement is critical to any business’s success. As a result, it’s surprising that the manufacturing industry has only a 25% engaged workforce.
2020 did nothing to help the organizational structure in manufacturing industries; in fact, it amplified the lack of engagement. Things flew out the window once the pandemic was fully underway. Due to stringent rules, communication became disorganized as shifts were continually changing. Employees are always waiting by the phones to find out if they have a job or if there are any new developments. Employee engagement in manufacturing industry has reached an all-time low.
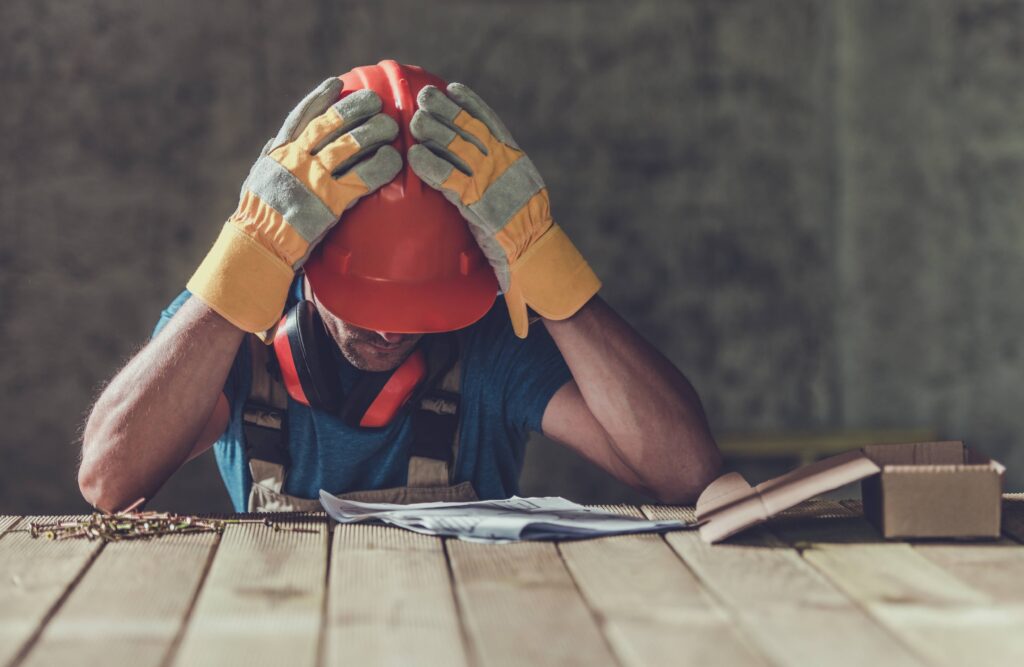
Employees sought that feeling of security once the pandemic restrictions were lifted and people returned to work. However, outdated communication methods such as phone calls, texts, and emails, as well as heaps of manual paperwork, prevent this. In the new decentralized reality, it simply does not work!
As the pandemic spread, safety procedures shifted dramatically. The pandemic only amplified the existing problems in manufacturing, which already had a low level of employee engagement. Employees with low engagement may be more likely to break safety regulations unintentionally, raising the risk of incidents to themselves and others around them. As a result, companies are looking for new ways to engage in manufacturing.
Managers understand the importance of acting quickly to boost employee engagement, especially in these trying times.
Impact Of Employee Engagement In Manufacturing Industry
Low employee engagement in manufacturing industry have an adverse effect on many parts of the organizational culture in manufacturing industries, but it’s particularly costly when it comes to employee retention. Companies should play a part in 150 percent of a worker’s annual salary when calculating the cost of turnover. Low motivation and productivity, for example, can lead to accidents and unsafe behavior.
Companies must find engagement solutions that ensure long-term growth, economic stability, and employee satisfaction, but COVID-19 has cut the time it would have taken manufacturers to develop such a program in half. So, how do you engage employees in the manufacturing industry? How can employee morale be improved in manufacturing?
Why Is Employee Engagement In Manufacturing Important?
It isn’t just about communication; it’s also about participation. As leaders and managers, we have a plethora of options for interacting with employees, but we don’t always use them to their maximum potential to engage employees in the manufacturing industry.
You must be thinking, “Why does it make a difference if my workers are engaged or not?”
When employees are disengaged, sales are lost, production is lost, productivity is low, and labor turnover rates are high. What evidence do we have for this? Employees who are disengaged cause $450-550 billion in losses each year in the United States.
Take a moment to absorb that.
“Engaged employees tend to yield better business results than non-engaged ones – across industries, company sizes, and nationalities, and in changing economic situations.”. – Gallup
There are a plethora of opportunities for businesses among the remaining workforce who are completely disengaged on the job. It would be a huge boost in productivity and sales for your firm if you could reduce that number by just 7%.
Based on the data, there’s a good chance you can improve employee communication and engagement.
How Do You Engage Employees In Manufacturing?
Here are some of the easiest ways to engage employees in the manufacturing industry:
1. Make Your Workers Feel Valued
The significance and positive influence of recognition cannot be overstated. Taking the time to celebrate small victories each week will boost your team’s happiness and motivation level.
Numerous studies support these claims.
For instance, workers who felt appreciated, were more than four times more likely to report high engagement levels (59 percent vs. 13 percent) and were less inclined to say they were stressed out on a regular workday, according to a recent 2021 study of manufacturing workers (16 percent vs. 66 percent ). That’s pretty amazing!
People like to feel appreciated by their employers for their significant time investment. In other words, they don’t want to be swept under the rug or to believe that they can be replaced. People need to feel as if their unique skills and even personalities contribute to the team’s success.
As a result, never forget to express gratitude for your employee’s presence. The purpose is to ensure that everyone’s unique contribution is seen and highlighted regularly, whether it’s for their specific talents or their knack for making jokes and keeping team spirits high.
2. Make Recognition & Rewards A Routine
Implementing rewards and employee engagement activities in Indian manufacturing companies foster a culture of satisfaction and loyalty. Positive work environments built on mutual respect and trust are more efficient and profitable.
Furthermore, devoting time and effort to employee recognition demonstrates to your workforce that their efforts are appreciated daily. Employee appreciation and recognition can be as simple as writing a handwritten thank you note or making a public announcement about one of their accomplishments.
3. Be Innovative While Making Use Of Incentives
Employees value non-cash incentives and rewards, according to controlled research studies.
Non-monetary incentives are remembered more than monetary ones, and the former has a greater impact on employee engagement and retention. A rewards program does not require a large budget to implement. There are cost-effective options available!
4. Listen To Your Employee
Workers and operators have the most hands-on expertise and a real-time view of what is happening on the production line in the manufacturing industry.
As a result, it should be self-evident that their input is hugely beneficial, particularly when considering improvements and fixes to existing processes. Allowing employees to know that you are willing to listen to their suggestions builds trust and respect.
5. Make Recognition & Rewards Available To Every Worker
It’s not just management or top-performing employees who need to be rewarded. You’re encouraging everybody in your company to do their best work and set specific goals for themselves by doing so. Positive behaviour will only inspire more of them among your employees.
6. Make Socializing An Important Event
Providing opportunities for employees to socialize and get to know one another as people (rather than just coworkers) will aid in the development of connections at all levels and will most likely improve collaboration and productivity.
7. Promote Health & Safety Programs For Workers
The word “training” rarely elicits much enthusiasm. However, you understand how critical it is to reduce the risks in the operation of industrial machines and to ensure worker health and safety. With immediate motivating factors and potential payoffs, a recognition program can help you boost morale. Motivate your employees and help them improve their performance.
The manufacturing industry is experiencing a severe skills shortage. Employers, on the other hand, have options for dealing with this. Manufacturing companies must keep up with modern recognition strategies and offer a high-quality program that sincerely engages existing employees while also attracting potential future ones.
How To Motivate Production Line Workers?
Here are some ideas for motivating your factory workers and getting your production line running smoothly:
Promote One-On-One’s For Factory Workers
Most manufacturing firms have a one-way internal communications plan, which means that management can send information to the employees but not back up the corporate ladder.
The structure of operational communication resembles a pyramid. Official statements and mandates are at the top and ripple down to the rest of the organization. The team and department communication are in the center. This is where work is frequently coordinated and assigned across organizational functions. Finally, there’s one-on-one communication. The real work is at the bottom of the communication pyramid.
That’s where your factory employees gather to resolve issues, overcome operational problems, and learn from one another to develop the skills.
This is where your managers can get a true understanding of the business’s day-to-day processes. Solving a slew of minor issues has a far bigger effect than addressing a few major issues. Ensure that the organization promotes bottom-up communication to capitalize on that priceless institutional knowledge.
Find Ways To Streamline Processes & Save Time
A factory worker may spend up to three hours per week searching for the information they require to perform their duties.
That’s disheartening. It suffocates motivation (as well as the soul) more quickly than almost anything. Factory workers have no easy way to find, manage , or store the information and resources they require for their jobs.
The majority of traditional forms of data sharing for manufacturers are difficult to scale and standardize. For guidance and information exchange, employees frequently have to rely on neighboring coworkers. However, an increasing number of manufacturers are moving to mobile-friendly digital workplaces.
Morale on your production line will improve, and motivation to do their best will follow shortly if you provide them with the knowledge they need to do their jobs in a faster, better, and easier way.
Provide Training and Upskilling Opportunities
Manufacturing’s most precious assets are its remaining employees, given the massive migration of the baby boomer generation from the workforce. They are a crucial resource that is currently keeping the manufacturing industry afloat. These factory workers will need to acquire new skills as the scope of their employment shifts away from traditional hands-on production.
Manufacturers invested $26.2 billion on internal and external training initiatives for new and existing factory workers in 2020, according to the Manufacturing Institute.
The manufacturing industry’s growth will necessitate new skills and technical knowledge. Invest in your workforce’s career development, and your production line will become more emotionally invested in the company.
Make Health and Safety Information A Priority
Manufacturing companies should prioritize safety, particularly now that COVID-19 requires them to implement new safety regulations quickly.
Some frontline workers say they’re “nervous ” about returning to work as states begin to revive their economies (and factories).
A digital workplace can help your factory workers feel more at ease about returning to work. You can use real-time communication to keep your employees up to date, informed, and reassured, which will keep them driven as they return to work.
Get An Engaged Workforce For The Long Haul With Zimyo
When you want to help your employees live their best lives and encourage innovation, you can achieve employee engagement in manufacturing. With Zimyo’s employee engagement software for manufacturing industry you can expect to boost company engagement, and enjoy real benefits of better business results.
With Zimyo, you don’t just get a tool to track those engagement levels. You get a complete communication and engagement platform that includes amazing features like employee recognition, mood-o-meter, announcements, discussion & break rooms along with an exceptional customer support that not only helps boost the success of your company but also your employees, long term.
The goal is to use our employee engagement software for manufacturing industry to not only accomplish their production floor goals but pair it with their workers’ day-to-day lives.
With that philosophy, they can experience improved employee productivity, high employee satisfaction, increase retention, decrease attrition, lower costs, and higher ROI for employee engagement programs.
When managers put forth their best efforts to ensure that employees have a positive employee journey, businesses will see a boost in employee engagement in manufacturing.
Also Read: Employee Engagement Software For Healthcare Industry